Making Lean Work
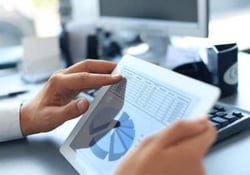
Lean failures are unfortunately about as common as Lean success stories. I was contracted to start up Lean in one department that upon first walk through showed Final Assembly of multiple retail products:
-
- Performed on dirty floor – tough ergonomics
- Dark, crowded, remote
- Work Instructions for many dozens of products were torn and marked up aged stapled copies placed on the floor by the product components
- Needed tools were shared with other departments
- Throughput was low, huge wasted labor hours during the 2-5 changeovers each day
- Under a layer of grime on the wall was a 5S reminder sign
All of the above made the area a challenge to supervise & retain people, increased product costs, slowed the conversion of cash into revenue and did not help to make quality products.
Lean can be effectively applied in a variety of ways. The Lean process applied was:
-
- Attain Top Management long term buy-in and commitment to Lean as an emerging participatory company culture and not a few months’ project with a start and an end. A scope is defined for where to start, what can success look like, where, how and for the measurement of progress.
- Learn Intro to Lean – classroom style with presentation, the mix of management & hourly is handpicked to include attitude, familiarity with target area and aptitude to help sell the Lean process internally.
- Learn 6S – class room style, with the Kaizen area in mind including starting metrics and pictures.
- Apply new skills in a Kaizenette™, a limited scope (smaller), shorter duration Kaizen – teach by example on shop floor at a work cell or office department, team usually, output: about 50 opportunities for improvement is fairly common.
- Lead the team through prioritization of opportunities, assign, execute; meet & track progress.
- Close out with team; capture improvement metrics & pictures; publish results to team, management and company; celebrate with team; market the results internally.
- Repeat with next team, adapting the process; get multiple teams going, select the best for training on additional Lean or quantitative tools – these become our internal leaders to sustain Lean culture and results.
The results in the case above were dramatic with product flow at a clean, convenient work height, instructions for each assembly station on monitors above the movable material carts, adequate lighting, tools at point of use, line changeover in minutes, better flow through the area and much more. Getting more product out with the same effort (and with less frustration) fostered pride in the team. Throughput was up by 2/3rds that met goals of: shortened lead times, delivery due dates and positioned company for growth! Area became a show point for customer tours instead of being avoided. A year or two later the area was again improved (Shine or refine reapplied from 6S).
Your internal Lean expert can tweak the above numbered steps or a consultant can adapt, train, coach and guide through the start of your Lean journey. Top accolade for a consultant is to find the company can sustain Lean on its own. The above has been successfully applied to quality production in Amish shops, molding, and machining to agriculture’s harvest and pack.
Please contact us if you would like to discuss further.
This article was written by Ty Haines, President, Manufacturer Solutions, LLC. Ty has spent 40 years in the manufacturing industry holding positions from Production Supervisor to President.